Hardwood Lumber Drying
- September 13, 2024
- 0 comment
hardwood lumber Drying is a critical step in wood processing that directly influences the quality, durability, and usability of the final product. Achieving the correct moisture content is key to preventing defects such as warping, cracking, and shrinking, ensuring that the lumber is perfectly suited for various uses, including furniture production, construction, and other woodworking projects.
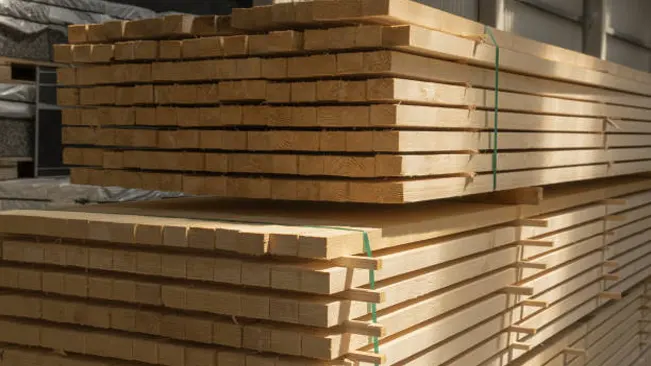
It’s essential to understand the importance of proper drying techniques, how to reach the ideal moisture levels, and strategies for preserving wood quality throughout the drying process. These aspects are vital for maintaining the integrity and performance of the wood in its final applications.
Understanding the Importance of Moisture Content
Moisture content (MC) in hardwood lumber refers to the amount of water in the wood relative to its dry weight. Controlling MC prevents wood deformities, ensuring stability in various environments for effective use.
Typically, the target moisture content for hardwoods depends on their intended use. For interior applications like furniture or flooring, lumber is usually dried to 6-8% moisture content, while for outdoor applications, slightly higher levels (around 12-15%) may be acceptable.
Wood that hasn’t reached the correct moisture level may cause issues during construction, finishing, or even when the product is already in use.
Key Terminology in Hardwood Lumber Drying
Before delving into drying methods, it’s essential to understand a few key terms related to the process:
- Moisture Content (MC): This refers to the amount of water present in the lumber, expressed as a percentage of the wood’s dry weight. For hardwoods, the target MC varies depending on the wood’s intended use. For interior applications like furniture, the MC should be between 6-8%, whereas outdoor lumber can maintain a higher MC of 12-15%.
- Equilibrium Moisture Content (EMC): This is the point where the wood stops absorbing or releasing moisture because it has balanced with the surrounding environment’s humidity and temperature.
- Fiber Saturation Point (FSP): This is the stage where all free water has evaporated from the wood, and only bound water remains in the wood’s cell walls. The FSP is around 28-30%, and drying beyond this point reduces the wood’s shrinkage and prepares it for further use.
- Dry Bulb and Wet Bulb Temperatures: These temperatures are critical in kiln drying, as they help control the environment within the kiln. The dry bulb measures the air temperature, while the wet bulb reflects the cooling effect of moisture evaporation.
Drying Methods for Achieving Optimal Moisture Content
Different drying methods offer various benefits depending on the wood species, available resources, and the desired drying speed.
1. Air Drying
Air drying is the most traditional method, where lumber is stacked in a well-ventilated area and left to dry naturally.
While this method is cost-effective and energy-efficient, it is slow, often taking several months to years, depending on the wood thickness and species. Air drying works well in moderate climates but may not always achieve consistent MC, particularly in humid environments.
2. Kiln Drying
Kiln drying is a fast, controlled process using heat, humidity, and airflow to dry lumber in days or weeks.
This method ensures precise moisture control, reducing defects like warping or cracking. Although energy-intensive and costly, it’s ideal for large-scale operations due to its efficiency and consistent results.
3. Pre-Dryer and Dehumidification Kilns
Pre-dryers are often used to lower the MC before placing the wood into a traditional kiln, balancing energy efficiency and drying speed. Dehumidification kilns use lower temperatures and recycle heat and moisture, making them more energy-efficient than conventional kilns.
4. Solar Kilns
Solar kilns harness solar energy to dry lumber, making them eco-friendly and cost-effective. However, solar kilns require careful monitoring to avoid over-drying or under-drying, and they are best suited for small-scale operations in sunny climates.
Achieving Optimal Moisture Content
To achieve optimal moisture content, it is essential to consider the wood species, the drying method, and the end use of the lumber. Here’s how you can ensure that your hardwood lumber is properly dried:
1. Monitor Moisture Levels
Use a moisture meter to check the MC regularly during drying. It’s important to test multiple boards, especially if using air drying, as the moisture content can vary depending on exposure to air and temperature.
2. Control the Drying Environment
For both kiln and air drying, control the drying rate to avoid drying the wood too quickly, which can cause surface cracking or case hardening (where the surface dries faster than the core). In kiln drying, gradually increasing the temperature and adjusting humidity levels will help the wood dry evenly.
3. Acclimatization
After drying, the wood should acclimate to the environment where it will be used. This helps prevent rapid moisture changes that can cause warping. For interior applications, acclimatize wood in the indoor space for a week or more before installation.
Tips for Maintaining Wood Quality During Drying
Maintaining wood quality during the drying process is essential for achieving the best results. Follow these tips to minimize defects and ensure even drying:
Proper Stacking
When stacking lumber for air drying or loading it into a kiln, ensure there are sufficient spacers (stickers) between boards to allow for airflow. Boards should be stacked evenly to prevent warping.
End Sealing
Hardwood boards often lose moisture faster at the ends, leading to splitting. Applying end-sealing products, such as wax or paint, can slow moisture loss and reduce the risk of end cracks.
Regular Monitoring
Throughout the drying process, periodically check for defects such as checks (surface cracks), cupping, or bowing. Identifying problems early can help you make adjustments and salvage the wood.
Common Challenges in Hardwood Lumber Drying
Achieving optimal moisture content is not without its challenges. Some common problems include:
- Uneven Drying: Particularly in air drying, external conditions like humidity and temperature fluctuations can lead to uneven drying, with some boards drying faster than others.
- Surface Cracking: Rapid drying, especially in kiln drying, can lead to cracks on the surface of the lumber. Reducing temperature or slowing down the drying process can mitigate this issue.
- Warping: Warping occurs when the wood dries unevenly, causing parts of the board to shrink at different rates. Proper stacking and controlling airflow can help reduce this issue.
The Role of Technology in Moisture Content Management
In modern wood processing, technology plays a crucial role in managing and controlling moisture content effectively. Advanced kilns now use computerized systems to regulate temperature, humidity, and airflow, ensuring uniform and consistent drying. These systems not only speed up the drying process but also minimize defects by precisely controlling the conditions inside the kiln.
Additionally, digital moisture meters with real-time sensors provide accurate readings, allowing woodworkers to monitor moisture levels closely and adjust drying conditions as necessary to achieve optimal results.
Conclusion
Achieving optimal moisture content in hardwood lumber is essential for producing high-quality, durable wood products. Whether air drying or kiln drying, understanding the drying process, using the right tools, and carefully monitoring moisture levels will help you avoid common defects like cracking and warping.
By following best practices and leveraging modern technology, you can ensure that your hardwood lumber reaches the desired moisture content, enhancing its value and performance for a wide range of applications.
Frequently Asked Questions (FAQ’s)
- What is the ideal moisture content for hardwood lumber?
The ideal moisture content for hardwood lumber used indoors is between 6-8%. For outdoor use, lumber generally requires a moisture content of around 12-15% to accommodate changes in humidity. - How can I measure the moisture content of hardwood lumber?
A moisture meter is the most reliable tool for measuring moisture content in wood. It provides an accurate reading, allowing you to monitor the drying process and ensure the wood is ready for use. - How long does it take to air dry hardwood lumber?
Air drying hardwood lumber can take anywhere from several months to over a year, depending on the species, thickness, and local conditions. Patience is key, as rushing the process may cause defects like warping or cracking. - What are the main benefits of kiln drying over air drying?
Kiln drying speeds up the drying process significantly, often reducing the time to just days or weeks. It also offers precise control over temperature and humidity, ensuring more consistent and high-quality results. - How do I prevent hardwood lumber from warping during the drying process?
Proper stacking with spacers to allow airflow and evenly distributing weight across the boards can prevent warping. Controlling the drying rate by avoiding rapid moisture loss is also critical to maintaining the wood’s stability. - Can drying hardwood lumber too fast cause damage?
Yes, drying wood too quickly can lead to surface cracks or case hardening, where the outer layers dry too fast, creating internal stress. This can result in weakened, unusable lumber if not addressed properly. - Is it necessary to acclimate hardwood lumber before using it?
Yes, it’s essential to acclimate dried lumber to the environment where it will be used. This process typically takes a week or more and prevents sudden moisture changes that can lead to warping or cracking. - What is the difference between air drying and kiln drying?
Air drying uses natural air flow and takes longer but is more energy-efficient. Kiln drying is much faster, providing precise control over the environment but requires significant energy input. - How can I ensure consistent moisture content across all boards?
Consistency is achieved by using proper stacking techniques with evenly spaced stickers for airflow. Regularly checking moisture content across different parts of the stack ensures even drying throughout. - What are the most common problems encountered during hardwood lumber drying?
Common issues include warping, cracking, and uneven drying, which often result from improper stacking or drying too quickly. Careful monitoring and adjusting drying conditions can help mitigate these problems.
James Wilson
Forestry AuthorJames Wilson has over 15 years of experience in forestry economics, specializing in sustainable practices, investment opportunities, and financial management. He has contributed to notable publications like "Forestry Today" and "EcoFinance Journal" and is known for providing practical and insightful advice. With a degree in Environmental Economics, James stays updated through continuous learning and active participation in industry discussions. Outside work, he enjoys hiking and nature photography, bringing a well-rounded perspective to his professional role.
Leave your comment