4 Types of Welding Explained: MIG vs TIG vs Stick vs Flux Core
- February 14, 2024
- 1 comment
Discover the key differences between MIG, TIG, Stick, and Flux Core welding. Learn which method suits your project best in this concise guide. Welding: the art and science of joining metals. Over the years, I’ve had the chance to experiment with various welding techniques, each with its unique flair, challenges, and applications. In this blog, I’ll share my experiences and insights into four popular welding methods: MIG, TIG, Stick, and Flux Core. I’ve assessed them based on ease of use, versatility, weld quality, and cost-effectiveness, hoping to guide fellow enthusiasts and professionals in choosing the right method for their projects.
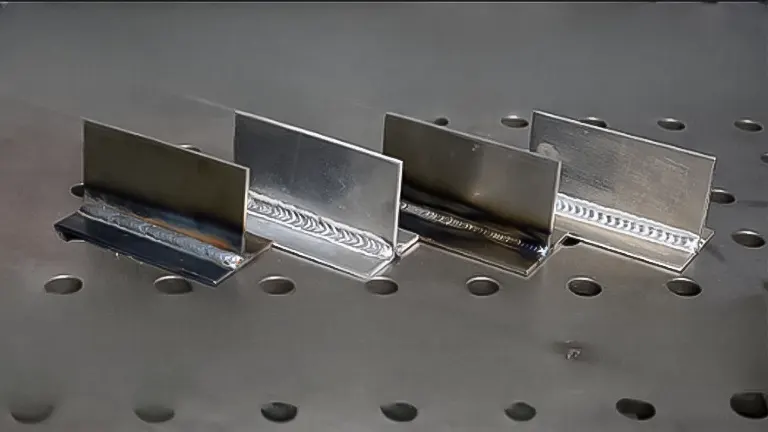
List of 4 Types of Welding Explained:
- MIG Welding (Metal Inert Gas)
- TIG Welding (Tungsten Inert Gas)
- Stick Welding (Shielded Metal Arc Welding)
- Flux Core Welding (Flux Cored Arc Welding)
Deciphering Welding Techniques: A Detailed Guide
Welding, an essential fabrication technique with millennia of history, plays a pivotal role in constructing and creating a vast array of items from swords to ships, and furniture. The choice of welding method is critical, with each offering unique advantages and suited to specific tasks.
As you delve into welding, you’ll discover that while some methods are straightforward and quick to pick up, others demand a more extended learning curve, requiring years to fully master.
Moreover, the suitability of welding types varies with the environment, with certain techniques being more conducive to indoor settings, whereas others excel outdoors. This guide aims to shed light on the diverse welding processes available, helping you identify the most appropriate technique based on your level of expertise and the specific materials you intend to weld.
Common Types of Welding and Their Characteristics
- MIG Welding (Metal Inert Gas Welding): Known for its ease of learning and versatility, MIG welding is suitable for a wide range of applications and materials. It delivers clean welds with minimal cleanup but incurs higher operational costs due to the need for shielding gas.
- TIG Welding (Tungsten Inert Gas Welding): Demanding a higher skill level, TIG welding is prized for its precision and the high-quality, aesthetically pleasing welds it produces. It’s exceptionally versatile, capable of welding more types of metals than other methods, though it’s slower and more time-consuming.
- Stick Welding (Shielded Metal Arc Welding): Renowned for its robustness and simplicity, stick welding is highly effective in outdoor or rugged environments. It can handle rusty or dirty materials well but requires a certain level of skill to achieve clean welds and involves more cleanup due to slag production.
- Flux Core Welding (Flux Cored Arc Welding): Offering a practical alternative to MIG welding when external gas isn’t feasible, flux core welding is faster in certain scenarios and doesn’t require a shielding gas. However, it generally produces rougher welds and more smoke, necessitating adequate ventilation.
Each welding method has its place, depending on the project requirements, available resources, and the welder’s proficiency. Whether you’re starting out in the welding field or looking to expand your skills to include more advanced techniques, understanding the pros and cons of each method is crucial in choosing the most suitable one for your needs.
Understanding the Various Welding Methods
The realm of welding is broad, encompassing several techniques each designed for particular applications and skill levels. Selecting the right welding approach involves evaluating your experience and the materials you plan to join. Some welding methods are known for producing neat, clean welds that necessitate minimal post-weld cleanup, while others are characterized by more substantial welds, generating a significant amount of slag that requires cleaning. Additionally, while certain welding techniques are limited to ferrous metals, others boast a more versatile application range. Below is an overview of common welding types, complete with their advantages and drawbacks, to guide your selection process.
1. MIG Welding (Metal Inert Gas)
In my personal journey through the diverse world of welding, MIG welding stands out as an exceptionally adaptable and user-friendly technique, akin to the Swiss Army knife in its versatility and reliability. This method has proven to be remarkably easy to grasp for beginners, yet it retains its value for experienced welders due to its effectiveness across a broad spectrum of applications.
Whether I’m working on delicate projects involving thin sheet metals that require precision and care, or tackling the challenges of joining thicker structural components where strength and durability are paramount, MIG welding has consistently delivered high-quality results.
Its inherent efficiency not only speeds up the process but also ensures a level of consistency and reliability that is crucial for both small-scale personal projects and larger, more complex professional undertakings. The ability to seamlessly adjust to the demands of different materials and thicknesses without compromising on quality or efficiency is what truly sets MIG welding apart as a cornerstone technique in my fabrication arsenal.
Quantitative Measurements
- Speed Advantage: MIG welding is noted for its remarkable speed, capable of completing welds up to three times faster than TIG welding on comparable tasks. This rapid pace directly translates to a significant reduction in project timelines, enabling quicker turnovers and increased productivity.
- Efficiency Gains: The efficiency of MIG welding not only lies in its speed but also in its ability to deliver consistent, high-quality welds with less effort. This efficiency minimizes the need for do-overs or corrections, further reducing labor hours and material waste on projects.
- Cost Reduction: By dramatically cutting down on labor time, MIG welding offers a notable decrease in overall project costs. The faster welding process allows for a more efficient use of resources, including labor and materials, making it a cost-effective choice for both small-scale and large-scale welding projects.
Pros
- Ease of Use: Ideal for beginners. The continuous wire feed makes for a straightforward welding process.
- Speed: Excellent for production work where time is of the essence.
- Versatility: Capable of welding various types and thicknesses of metals.
Cons
- Cost: The need for shielding gas can increase operational costs.
- Weld Appearance: While functional, MIG welds might not be as aesthetically pleasing as TIG welds.
2. TIG Welding (Tungsten Inert Gas)
Venturing into TIG welding has required significant dedication, involving a steep learning curve to master the skills necessary for high-level welding work. This technique calls for precise control over the welding torch and filler material, alongside consistent management of the arc’s distance from the workpiece.
The outcomes of becoming proficient in TIG welding are substantial, as it delivers unparalleled weld precision and quality. For projects where both the look and the strength of the weld are crucial, TIG welding is the preferred method. It enables the creation of clean, robust, and aesthetically pleasing welds, making it essential for a wide array of applications, from customizing vehicles to crafting detailed metal artworks.
The precision and control afforded by TIG welding allow for tackling projects that demand a high degree of craftsmanship, positioning it as more than a mere welding technique but rather a form of artistic expression.
Quantitative Measurements
- Accuracy and Precision: Quantitative measurements are crucial for ensuring accuracy and precision in various fields, from engineering to science. They allow for the exact quantification of variables, enabling precise comparisons, calculations, and evaluations.
- Performance Metrics: In many industries, quantitative measurements serve as key performance indicators (KPIs), helping assess the efficiency, productivity, and quality of processes, products, or services. These metrics are essential for informed decision-making and strategic planning.
- Statistical Analysis: Quantitative data is fundamental for statistical analysis, providing a solid basis for testing hypotheses, identifying trends, and making predictions. It supports the objective analysis of patterns and relationships within data sets.
Pros
- Precision: Offers control over the weld bead size and heat input.
- Weld Quality: Produces high-quality, clean welds with minimal spatter.
- Versatility: Suitable for more types of metals than any other method.
Cons
- Learning Curve: Requires significant skill and practice.
- Speed: Much slower than MIG, making it less ideal for lengthy production runs.
3. Stick Welding (Shielded Metal Arc Welding)
Stick welding has consistently proven itself as a dependable method for tackling outdoor and heavy-duty tasks. Its straightforward nature and durability are particularly well-suited for executing repairs and construction projects where conditions are far from perfect.
The technique’s resilience against environmental challenges and its ability to handle a variety of materials make it a go-to choice for work in settings that might compromise other, more sensitive welding processes.
This reliability, coupled with the minimal setup and equipment requirements, establishes stick welding as a preferred option for those faced with demanding project conditions or seeking a robust solution for outdoor applications.
Quantitative Measurements
- Comparative Speed: Although stick welding doesn’t match the rapid pace of MIG welding, it strikes an effective balance between speed and adaptability. Its performance remains consistent across a range of environments, especially where conditions might hinder other welding methods.
- Environmental Adaptability: Stick welding distinguishes itself in challenging conditions, such as windy or outdoor settings, maintaining effectiveness where more sensitive processes could be less reliable. This resilience adds to its versatility and broad applicability.
- Versatility in Use: Offering a versatile solution across various materials and conditions, stick welding supports a wide array of applications from construction to repair, highlighting its utility in scenarios that demand both robustness and a degree of mobility.
Pros
- Durability: Equipment is simple and rugged, perfect for harsh environments.
- Versatility: Effective on dirty or rusty materials.
- Cost-Effective: No need for gas, making it more economical in certain situations.
Cons
- Skill Level: Requires good technique to achieve clean welds.
- Cleanup: Produces more spatter and requires slag removal after welding.
4. Flux Core Welding (Flux Cored Arc Welding)
Flux core welding has significantly altered my approach to projects requiring quick execution and flexibility. Functioning similarly to MIG welding but without the dependency on external shielding gas, it stands out for its robustness and efficiency.
This method has proven to be particularly valuable in environments where setting up gas cylinders is impractical, allowing for a seamless welding process that maintains high productivity levels.
Its capacity to adapt to various settings without compromising on speed or quality makes flux core welding a preferred choice for tasks that demand both reliability and the ability to work under less controlled conditions.
Quantitative Measurements
- Deposition Rate: Flux core welding showcases a superior deposition rate compared to MIG welding, enhancing its speed and efficiency in numerous welding scenarios. This attribute makes it especially suitable for projects requiring rapid progress and high productivity.
- Effectiveness with Thick Materials: The technique excels when working with thick materials, where its higher deposition rate ensures deeper penetration and stronger welds. This capability is crucial for heavy-duty applications and structural projects demanding robust joins.
- Out-of-Position Welding Proficiency: Flux core welding is notably effective for out-of-position welding tasks, such as vertical or overhead welds. Its versatility and the ability to maintain quality welds in challenging positions offer significant advantages in complex welding situations.
Pros
- No Gas Needed: Can be more cost-effective and convenient, especially outdoors.
- High Penetration: Excellent for welding thick materials.
- Speed: Comparable to MIG, with some advantages in specific applications.
Cons
- Weld Appearance: Can be rougher than MIG or TIG welds.
- Fumes: Produces more smoke and fumes, requiring good ventilation.
Related Articles:
- First Welder Guide for DIYers: Practical Tips
- Best 5 MIG Welders: From Budget-Friendly to Premium Picks
- Best Black Friday Welding Machine Deals 2023
- Troubleshooting Common Welding Machine Problems
- Best Cheap MIG Welder on Amazon
- Best Yeswelder Plasma Cutter
- Best MIG Welder by YesWelder
- Best STICK Welder by YesWelder
- Best 110v MIG Welders
- Best 120V MIG Welders
Conclusion
Each welding method has its niche, when it comes to selecting the appropriate welding technique, the decision hinges on the specific requirements of the project, as well as the experience level of the welder. MIG welding stands out as an excellent option for those just starting out or for any welder prioritizing quickness and productivity across a diverse range of tasks.
On the other hand, TIG welding is the go-to method for projects where the focus is on achieving the highest level of precision and quality in the weld, particularly with thinner materials. For environments that are less controlled or for working with tougher materials, stick welding offers a sturdy and dependable solution, renowned for its effectiveness outdoors and with heavy-duty materials. Lastly, flux core welding emerges as a highly adaptable and efficient choice for situations where using external gas is impractical or impossible, providing a reliable alternative without sacrificing performance.
Frequently Asked Questions
- What is the main difference between MIG and TIG welding?
MIG welding uses a continuously feeding wire as the electrode and is generally faster and easier to learn, making it suitable for a variety of projects. TIG welding requires the welder to hold a non-consumable tungsten electrode in one hand and the filler material in the other, offering greater precision and control for high-quality welds. - Can Stick welding be used on all types of metals?
Stick welding is versatile and can be used on most common metals and alloys, including steel, stainless steel, and cast iron. However, it’s less suitable for welding thin metals or more exotic alloys compared to methods like TIG welding. - Is Flux Core welding good for beginners?
Yes, flux core welding is considered beginner-friendly due to its simplicity and the fact that it does not require an external shielding gas, making setup and operation relatively straightforward. - What materials can I weld with TIG welding?
TIG welding is known for its versatility and can be used on a wide range of materials, including but not limited to, steel, stainless steel, aluminum, titanium, and even some exotic metals. - Why choose MIG welding over other types?
MIG welding is often chosen for its speed, ease of use, and versatility across both thin and thick materials, making it ideal for a variety of applications from home DIY projects to professional manufacturing. - What are the advantages of Stick welding?
Stick welding is highly portable, does not require a shielding gas, and is effective in windy or outdoor conditions. It’s also capable of welding dirty or rusty metals, making it ideal for repairs and fieldwork. - How do I decide which welding method to use for my project?
The choice of welding method depends on several factors, including the type of material, thickness, the desired quality of the weld, working conditions, and your own skill level and equipment. - Can Flux Core welding be used outdoors?
Yes, flux core welding is particularly well-suited for outdoor use since it does not require external shielding gas, which can be disrupted by wind. - What safety equipment is necessary for welding?
Regardless of the welding type, essential safety equipment includes a welding helmet with proper eye protection, gloves, protective clothing, and adequate ventilation to avoid inhaling harmful fumes. - How can I improve my welding skills?
Practice is key to improving welding skills. Additionally, taking classes, watching instructional videos, and learning from experienced welders can provide valuable techniques and insights. Experimenting with different materials and welding methods can also enhance your versatility and proficiency.
We’re eager to hear from you! Dive into the discussion by sharing your own experiences and insights on the MIG, TIG, Stick, and Flux Core welding methods in the comments section below. Whether you’re a seasoned welder or just starting out, your perspectives could greatly benefit others navigating the world of welding. Help fellow enthusiasts and professionals alike by shedding light on your personal journey and recommendations. Your input is invaluable in helping others make well-rounded decisions in their welding endeavors!
Edward Smith
Forestry AuthorWoodworking is about more than crafting; it's a harmonious connection with nature, mastering tools, and preserving our environment. I'm here to share my knowledge and experiences with you, forging a future where we can embrace wood's beauty and utility while safeguarding our forests' health and diversity.
I am wanting to learn mig welding Can you direct me to a training programme suitable for older people Thankyou Jack Jones
Jack Jones
February 17, 2024 10:47 pm