MIG vs. TIG Welding: Exploring the Differences
- January 31, 2024
- 0 comment
Discover the key differences between MIG and TIG welding. Learn which technique suits your project best for optimal results and efficiency. Over the years, my journey as a welder has led me to cultivate a profound respect for the intricate details and subtle differences inherent in various welding techniques. Through this blog, I am eager to delve into and elucidate my personal encounters and learned perspectives regarding two of the foremost welding methods in the industry: Metal Inert Gas (MIG) and Tungsten Inert Gas (TIG) welding.
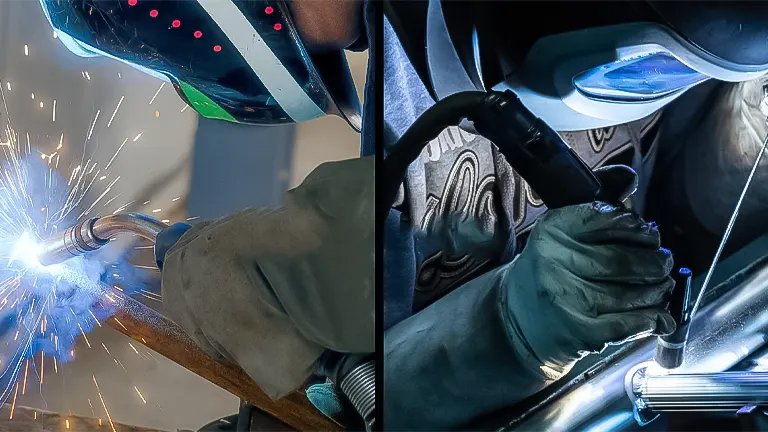
Each of these techniques possesses its own distinct allure and set of complexities. My experiences have taught me the critical importance of selecting the appropriate method, as it can dramatically influence the overall quality and productivity of the welding tasks at hand.
Table of Contents
- MIG Process
- MIG Advantages and Disadvantages
- TIG Process
- TIG Advantages and Disadvantages
- Performance Comparison
- Situational Suitability
Understanding the Basics: MIG and TIG at a Glance
Embarking on the welding journey, it’s essential to grasp the fundamental differences between Metal Inert Gas (MIG) and Tungsten Inert Gas (TIG) welding, each with its unique mechanics and applications. MIG welding, known for its user-friendliness, operates akin to a metalwork version of a hot glue gun. It employs a continuously feeding wire which serves a dual purpose: it acts as an electrode to create the arc and as the filler material to build the weld.
This wire is automatically fed through the welding gun, making MIG an efficient choice for long, uninterrupted welds. The process is further simplified as the welder only needs to control the gun’s movement and speed. In contrast, TIG welding is akin to an artist’s detailed brushwork in metal fabrication. It utilizes a non-consumable tungsten electrode to generate the weld’s heat. The welder, in a display of skill and precision, manually feeds a separate filler rod into the weld pool.
This meticulous process requires a steady hand and acute concentration, as the welder simultaneously manages the torch and the filler material. TIG’s methodical nature allows for intricate, high-quality welds on a variety of metals, making it a preferred choice for tasks demanding precision over speed. Understanding these core differences sets the foundation for appreciating the specific applications, advantages, and limitations of MIG and TIG welding in various contexts.
MIG Process
The Metal Inert Gas (MIG) welding process, also known in the industry as Gas Metal Arc Welding (GMAW), is a method that incorporates either a semi-automatic or fully automatic arc to forge a weld. This process is characterized by its use of a consumable wire electrode, which acts as the filler material, accompanied by a protective shielding gas. The primary function of this shielding gas is to safeguard the weld from atmospheric contamination, thereby enhancing weld penetration and minimizing porosity in the weld bead.
In the MIG welding setup, both the electrode and the shielding gas are channeled through the welding gun, sometimes referred to as a torch. A commonly used gas mixture for this purpose is composed of 75% argon and 25% CO2. However, this blend can vary based on the specific materials being welded, as well as other factors pertinent to the welding process.
Another key feature of MIG welding is the utilization of a continuous, consumable wire electrode, which is delivered through a lead to the welding gun. The selection of the wire electrode, including its composition and diameter, is tailored according to the types of metals being fused, the thickness of the parts involved, and the configuration of the joint. Additionally, the rate at which this electrode is fed into the welding zone is crucial and is governed by the Wire Feed Speed (WFS) settings. These settings are adjusted to ensure an adequate supply of weld metal for the joint, balancing the need for speed with the requirement for a solid, reliable weld.
MIG Advantages and Disadvantages
Advantages of MIG Welding
- Ease of Learning and Use: MIG welding is generally easier to learn and use, making it accessible for beginners. The process is more straightforward compared to other welding methods like TIG.
- Speed: MIG welding allows for faster welding compared to TIG or Stick welding. This is particularly beneficial in industrial settings where time efficiency is crucial.
- Efficiency: Due to the continuous wire feed mechanism, it offers high productivity as there is no need to frequently stop to replace electrodes, as is the case with Stick welding.
- Versatility: MIG welding can be used on a variety of metals and alloys, including carbon steel, stainless steel, aluminum, magnesium, and nickel alloys.
- Cleaner Welds: It produces less slag as compared to Stick welding, resulting in cleaner welds and less cleanup work post-welding.
- Control and Precision: Offers good control over the welding process, especially with thinner metals.
- Better Weld Pool Visibility: Since the process doesn’t generate slag, the welder can see the weld pool more clearly, enhancing precision.
Disadvantages of MIG Welding
- Cost of Equipment and Maintenance: MIG welders and the associated gear (like gas tanks) can be more expensive. Regular maintenance is also required to keep the equipment in good condition.
- Shielding Gas Dependency: The need for a constant supply of shielding gas can increase operational costs and may not be suitable for outdoor welding where wind can disperse the gas.
- Less Portable: Due to the need for a shielding gas bottle and external wire feed, MIG welding setups are less portable compared to Stick welding.
- Limited Suitability for Thick Materials: While MIG is excellent for thin to medium thickness materials, it may not be the best choice for extremely thick materials.
- Quality Issues with Improper Technique: If not done correctly, MIG welding can lead to problems like porosity, lack of fusion, or excessive spatter.
- Not Ideal for Overhead or Vertical Welding: Due to the use of a liquid weld pool, MIG welding can be more challenging in vertical or overhead positions.
- Environmental Limitations: MIG welding is less effective in windy conditions as the wind can blow away the shielding gas, leading to poor quality welds.
TIG Process
Tungsten Inert Gas (TIG) welding, also known as Gas Tungsten Arc Welding (GTAW), is a process that, like MIG welding, utilizes an arc for welding. However, TIG differentiates itself in a significant way: it employs a non-consumable tungsten electrode, in contrast to MIG’s consumable electrode.
Alongside this tungsten electrode, TIG welding requires a separate, consumable filler material, typically in the form of a rod. This rod is manually introduced into the weld pool, necessitating the use of both hands during the welding process—one to manage the tungsten electrode and the other to feed the filler rod.
In TIG welding, the choice of filler rod, including its composition and size, is meticulously selected based on the specific requirements of the weld being executed. Similar to MIG, TIG welding also relies on a shielding gas to protect the weld area.
However, TIG commonly uses 100% argon as the shielding gas, avoiding CO2 which is often used in MIG. The reason for this is that CO2 can lead to the formation of tungsten oxide, which might cause premature wear on the tungsten electrode and potentially contaminate the weld.
Another distinctive feature of TIG welding is the incorporation of a foot pedal. This pedal allows the welder to finely adjust the amperage, thus controlling the heat intensity during the welding process. This capability to modulate the heat input in real-time grants the welder exceptional control over the heat applied to the metal, which is crucial for achieving precision in the welds, particularly when working with delicate or thin materials.
TIG Advantages and Disadvantages
Advantages of TIG Welding
- Precision and Control: TIG welding offers superior control over the welding process, allowing for precise, intricate welds. This makes it ideal for detailed work or delicate materials.
- High-Quality Welds: It produces high-quality, clean welds with minimal spatter, making it suitable for applications where appearance is important.
- Versatility: TIG welding can be used on a wide range of metals, including steel, stainless steel, aluminum, nickel alloys, copper, brass, and even gold.
- No Flux or Slag: Unlike some other welding methods, TIG doesn’t require flux and doesn’t produce slag, which means no slag removal post-welding and better weld visibility during the process.
- Stronger and Cleaner Welds: The use of inert gas shields the weld from contamination, resulting in stronger and cleaner welds.
- Welding in All Positions: TIG welding can be effectively used in all positions – flat, vertical, horizontal, or overhead.
- Aesthetic Weld Appearance: Due to its precision, TIG welding often results in aesthetically pleasing welds, important for exposed surfaces.
Disadvantages of MIG Welding
- Cost of Equipment and Maintenance: MIG welders and the associated gear (like gas tanks) can be more expensive. Regular maintenance is also required to keep the equipment in good condition.
- Shielding Gas Dependency: The need for a constant supply of shielding gas can increase operational costs and may not be suitable for outdoor welding where wind can disperse the gas.
- Less Portable: Due to the need for a shielding gas bottle and external wire feed, MIG welding setups are less portable compared to Stick welding.
- Limited Suitability for Thick Materials: While MIG is excellent for thin to medium thickness materials, it may not be the best choice for extremely thick materials.
- Quality Issues with Improper Technique: If not done correctly, MIG welding can lead to problems like porosity, lack of fusion, or excessive spatter.
- Not Ideal for Overhead or Vertical Welding: Due to the use of a liquid weld pool, MIG welding can be more challenging in vertical or overhead positions.
- Environmental Limitations: MIG welding is less effective in windy conditions as the wind can blow away the shielding gas, leading to poor quality welds.
Performance Comparison
- Speed and Efficiency: MIG takes the lead here. It’s faster due to the continuous wire feed, making it ideal for long, uninterrupted welds. I’ve found it especially useful for larger projects where time is a factor.
- Precision and Control: TIG wins hands down. The level of control and finesse TIG offers is unparalleled, perfect for intricate and delicate welds. When working on a custom motorcycle frame, TIG was my go-to for its precision.
- Ease of Use: For beginners, MIG is more approachable. It’s relatively easier to learn and requires less hand-eye coordination compared to TIG.
- Material Versatility: TIG is more versatile when it comes to different types of metals, especially thinner gauges and non-ferrous metals. I’ve successfully used TIG on materials like magnesium and aluminum, which require a delicate touch.
Situational Suitability
- For Heavy-Duty Work: If you’re looking at structural projects or outdoor repairs, MIG is your ally. It’s less sensitive to wind and outdoor elements.
- For Artistic and Detailed Work: TIG’s precision makes it a clear choice for artists and those working on detailed metal fabrication.
Personal Recommendations
- For Automotive Work: I lean towards TIG, especially for custom jobs. The precision and finish are unbeatable.
- For General Fabrication: MIG is the go-to for its speed and efficiency. It’s excellent for building frames, gates, and general metal structures.
Related Articles:
- First Welder Guide for DIYers: Practical Tips
- Best 5 MIG Welders: From Budget-Friendly to Premium Picks
- Best Black Friday Welding Machine Deals 2023
- Troubleshooting Common Welding Machine Problems
- Best TIG Welder for the Money: Your Ultimate Buying Guide
- Best TIG Welder for Beginners
- Underwater Welding: Techniques, Risks, and Impacts on Structural Durability
- Best Welding Helmet 2024
- Practical Guide To Basic Welding Positions
Choosing the Right Tool for the Job
In my years of welding, I’ve learned that the choice between MIG and TIG often comes down to the specific requirements of the project. For quick, efficient work on thicker materials, MIG is my preferred method. But when I need precision and finesse, particularly on thinner materials, TIG is unrivaled.
Both MIG and TIG have their place in a welder’s arsenal, and mastering both has made me a more versatile and capable craftsman. The beauty of welding lies in the sparks, the heat, and the challenge of creating something strong and lasting. Whether it’s MIG or TIG, the joy of welding is in the journey and the skillful execution of each method.
Conclusion
Choosing between MIG and TIG welding boils down to the specific requirements of your project. For those starting out or working on large, less intricate projects, MIG is a great starting point. For the artisans and perfectionists who value precision and versatility, TIG is the way to go. Personally, having both in my arsenal has allowed me to tackle a wide range of projects with confidence and finesse. Remember, the best weld is not just about technique but understanding the material and the end goal of your project.
Frequently Asked Questions
- What are the primary differences between MIG and TIG welding?
MIG welding uses a continuously feeding wire that acts as both the electrode and the filler material, making it suitable for faster, longer welds. TIG welding uses a non-consumable tungsten electrode, and the welder manually feeds a filler rod into the weld pool, offering precision and control for detailed work. - Which is easier to learn for beginners, MIG or TIG welding?
MIG welding is generally considered easier for beginners due to its simpler process and the automatic feeding of the welding wire, requiring less coordination and skill initially. - Can MIG and TIG welding be used on all types of metals?
TIG welding can be used on a wider variety of metals, including thin and non-ferrous metals like aluminum and stainless steel. MIG welding is better suited for thicker materials and is often used for steel and aluminum but might not be as effective on very thin materials. - Is TIG welding stronger than MIG welding?
The strength of a weld depends more on the skill of the welder and the welding parameters than on the welding process itself. However, TIG welding can produce more precise and cleaner welds, which, in some cases, may lead to stronger welds due to better control over the heat and filler material. - What equipment is needed for MIG and TIG welding?
MIG welding requires a welding machine with a wire feed mechanism, a MIG gun, and shielding gas. TIG welding requires a TIG welder, a TIG torch, tungsten electrodes, filler rods, and shielding gas. - How do I choose between MIG and TIG welding for a project?
The choice depends on the project’s requirements, including the type of metal, thickness, precision needed, and the desired speed of completion. MIG is suitable for quick, larger projects and TIG for precise, high-quality welds on thinner materials. - Can MIG welding be used for thin materials?
While MIG welding can be used for thin materials, it requires a lot of skill to prevent burn-through. TIG welding is generally preferred for very thin materials due to its greater control over the heat input. - What are the safety considerations for MIG and TIG welding?
Both welding types require proper safety gear, including a welding helmet, gloves, and protective clothing. Proper ventilation is also crucial to avoid inhaling harmful fumes. TIG welding produces less spatter but requires more attention to UV exposure due to the intensity of the arc. - How does the cost of MIG and TIG welding compare?
TIG welding equipment and consumables can be more expensive due to the need for tungsten electrodes and a variety of filler materials. MIG welding is generally less costly upfront and might be more economical for projects requiring high-volume welds. - Can I switch between MIG and TIG welding on the same machine?
Some modern welding machines offer multi-process capabilities, allowing users to switch between MIG, TIG, and other welding processes. However, the effectiveness and convenience of switching depend on the specific machine and the welder’s skill level.
We’re eager to hear your thoughts! Share your personal experiences and insights on MIG vs. TIG Welding in the comments section below. Whether you’re a seasoned welder or new to the craft, your perspectives could greatly benefit others navigating the differences between these two welding techniques. Your input might just be the guidance a fellow enthusiast needs to make an informed decision for their next project!
Edward Smith
Forestry AuthorWoodworking is about more than crafting; it's a harmonious connection with nature, mastering tools, and preserving our environment. I'm here to share my knowledge and experiences with you, forging a future where we can embrace wood's beauty and utility while safeguarding our forests' health and diversity.
Leave your comment